Gearboxes are important but susceptible to wear and tear like any complex machinery, and their failure can have severe consequences, including costly downtime, safety hazards, and potential property damage. To mitigate these risks, regular inspections are crucial to identify and address potential issues early on, so we can ensure the continued reliability and safety of our hoists. This article will look into the essential steps involved in conducting a thorough hoist gearbox inspection.
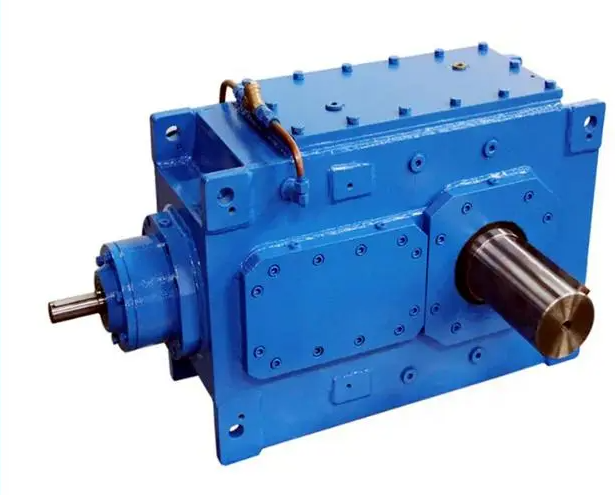
Hoist Gearbox Key Components and Their Potential Vulnerabilities
We have given you a guide about the working principles, selection, and maintenance tips of the hoist gearbox. To effectively inspect a hoist gearbox, it’s essential to understand its key components and their potential vulnerabilities.
- Gear Teeth: These interlocking components are responsible for transmitting power within the gearbox. Over time, gear teeth can experience wear, chipping, or pitting due to excessive load, misalignment, or inadequate lubrication. Visual inspection can reveal obvious damage, while listening for unusual noises like grinding or squealing can indicate more subtle issues.
- Bearings: Bearings support the rotating shafts within the gearbox, reducing friction and enabling smooth operation. Common types include ball bearings, roller bearings, and needle roller bearings. Signs of bearing wear include excessive vibration, noise, and increased temperature. Regular lubrication is crucial to prevent premature bearing failure.
- Seals: Seals are designed to prevent contaminants like dirt, moisture, and debris from entering the gearbox, while also retaining lubricant. Damaged or worn seals can lead to lubricant leakage, increased friction, and accelerated component wear. Inspect seals for cracks, tears, or hardening, which may indicate a compromised seal.
- Lubrication System: Proper lubrication is vital for the longevity and performance of a hoist gearbox. Lubricant provides a protective film, reduces friction, and dissipates heat. Signs of lubrication issues include excessive heat, unusual noise, and metal particles in the lubricant. Regular oil analysis can help identify potential problems early on.
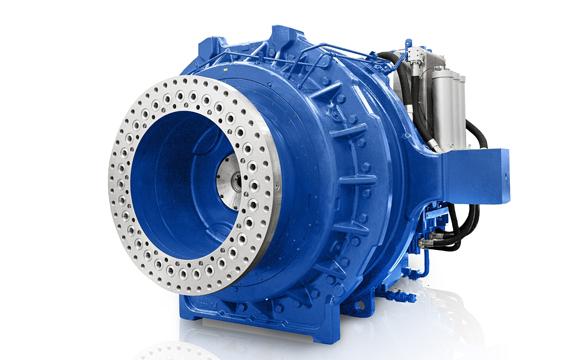
The Inspection Process of Hoist Gearbox
There may be many reasons for gearbox gear failure, which requires us to carefully inspect and maintain the gears. If you encounter a gearbox gear failure, you should first find out the specific cause and then take appropriate measures. In this way, we can better ensure the normal operation of the gear and extend the service life of the gearbox. The following will introduce several common reasons for the failure of the construction hoist reducer gear:
A comprehensive inspection of a hoist gearbox involves a combination of visual, auditory, and instrumental techniques.
Visual Inspection
A thorough visual inspection is the first step in assessing the condition of a gearbox. Look for signs of external damage, such as cracks, dents, or corrosion on the housing. Check for any leaks of lubricant, which could indicate a seal failure or internal damage. Additionally, inspect the alignment of the gearbox with other components, as misalignment can lead to excessive wear and vibration.
Listening Test
A trained inspector can often identify potential issues by listening to the gearbox while it’s in operation. Unusual noises, such as grinding, squealing, or humming, can indicate worn gears, damaged bearings, or other mechanical problems. By pinpointing the source of the noise, the inspector can narrow down the potential causes of the issue.
Temperature Check
Excessive heat is often a symptom of underlying problems within a gearbox. Using a non-contact infrared thermometer, the inspector can measure the temperature of the gearbox housing and individual components, such as bearings and gears. Elevated temperatures may indicate increased friction, inadequate lubrication, or misalignment.
Vibration Analysis
Vibration analysis is a powerful diagnostic tool that can help identify mechanical problems before they escalate. By using a vibration meter, the inspector can measure the vibration levels at various points on the gearbox. Excessive vibration can be caused by factors such as worn bearings, unbalanced rotors, or misalignment. By analyzing the vibration data, the inspector can pinpoint the root cause of the problem and recommend appropriate corrective actions.
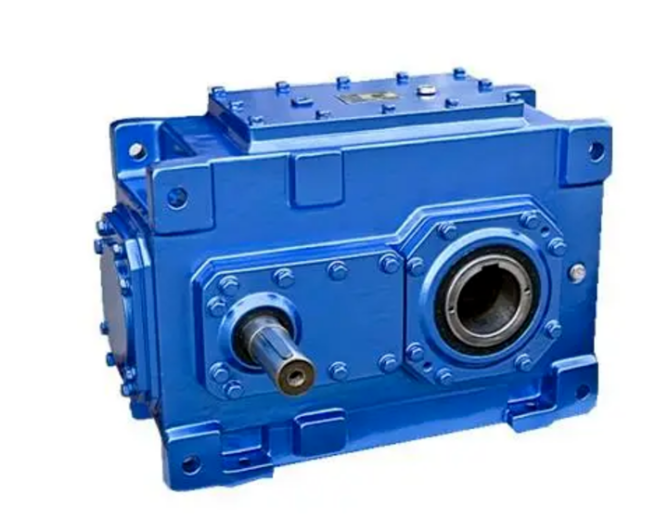
Common Gearbox Problems and Solution
Gear Tooth Wear
Gear tooth wear is a common issue that can lead to reduced efficiency, increased noise, and ultimately, gearbox failure. Excessive load, misalignment, inadequate lubrication, and material fatigue are common causes of gear tooth wear. The consequences of severe gear tooth wear include increased vibration, reduced load-carrying capacity, and potentially catastrophic failure. Repair options for gear tooth wear range from re-machining the gears to replacing them entirely.
Bearing Failure
Bearing failure can result from various factors, including inadequate lubrication, contamination, misalignment, and excessive load. Signs of bearing failure include increased vibration, noise, and elevated temperature. In some cases, the bearing may seize, causing damage to the shaft and other components. Replacement of the failed bearing is typically the only viable solution.
Seal Leakage
Seal leakage can lead to a loss of lubrication, increased friction, and accelerated wear of internal components. Additionally, contaminants can enter the gearbox, causing corrosion and further damage. Seal leakage can be caused by factors such as age, excessive temperature, mechanical damage, or improper installation. Repair options include replacing the damaged seal or repairing the seal groove.
Lubrication Issues
Inadequate lubrication can lead to increased friction, excessive heat, and premature wear of components. Conversely, excessive lubrication can result in contamination and reduced efficiency. It is essential to use the correct type and quantity of lubricant and to adhere to the manufacturer’s recommended lubrication intervals. Regular oil analysis can help identify potential lubrication issues and take corrective action.
Final Word
With the outlined in this article by CPTC, including visual inspections, listening tests, temperature checks, and vibration analysis, it is possible to maintain optimal gearbox performance and minimize downtime. Timely maintenance and proactive problem-solving are essential to prolong the life of your hoist gearbox and safeguard your operations.
Related Products
Yaskawa Inverter
Customizable Options;
Precise Speed Control;
Yaskawa inverter & Yaskawa inverter…
Motor for Construction Hoist
Gentle braking (by the…
Conductor Bar System
Stability and high…
Siemens Inverter
High performance
Automation
Reliability