The complex working environments of cranes necessitate careful selection of safe and reliable brake systems. As a core component, the performance of crane brakes directly impacts the daily operational efficiency and construction productivity of cranes. Therefore, it is of great significance to strengthen the selection and safety performance analysis of crane brakes.
This comprehensive guide will delve into the design principles, safety considerations, inspection procedures, and troubleshooting techniques for crane brakes. We will pay particular attention to crane brake components, brake coils, and the overall performance of crane brake systems.

Crane Brake Design Principles
In addition to the environmental conditions, factors such as load capacity and operating speed also affect the design of crane brakes. Typically, crane brakes are implemented with fail-safe friction electromagnetic brakes. Typical strong operations of motors and reducers make the use of fail-safe electromagnetic friction brakes economical. The following are some of the common types used in cranes:
- Disc brakes: These are among the most reliable and effective heat dissipating mechanisms which makes them common for use in cranes.
- Drum brakes: With their ability to provide high torque, drum brakes are widely utilized in heavy machinery for construction and mining.
- Electromagnetic brakes: As one of the fastest responding control devises, these can be used whenever precision control is required.
Safety Considerations in Crane Brake Selection
For standardized brakes, specific criteria must be followed regarding standardization, practicality, safety as well as legal and organizational requirements. These considerations are designed to minimize potential hazards during practical implementation.
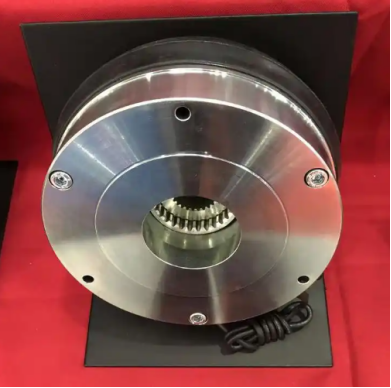
Standardization Principle
Considering the functionality of crane brakes across different applications, it is usual to opt for standard brakes unless there are special specifications for a certain crane project. The policies set by the state should be followed when picking one. In addition, the different models and types of cranes also have different specifications for their brakes which makes close attention to detail concerning the dimensions and specifications of the crane brake necessary. Deviations from standard dimensions may create difficulties with proper fitting as well as considerable safety hazards in operational functions.
Safety Principle
A primary consideration when selecting crane brakes is their safety performance in actual applications. The analysis of a crane brake’s practical performance is essential to ensure its reliability and safety. Given the heavy workload and large loads that cranes handle, the materials used in crane brake construction must meet stringent requirements for stiffness and safety. If conditions permit, performance testing, particularly for core components such as brake levers, brake arms, and springs, should be conducted to ensure compliance with national standards.
Compatibility Principle
As a core component of a crane, the brake is directly or indirectly linked to other components. Therefore, it is essential to carefully evaluate the compatibility of the crane brake with other components. During brake selection, full consideration should be given to the matching of various systems within the crane, and whether the brake meets compatibility standards, including system performance and application environment.
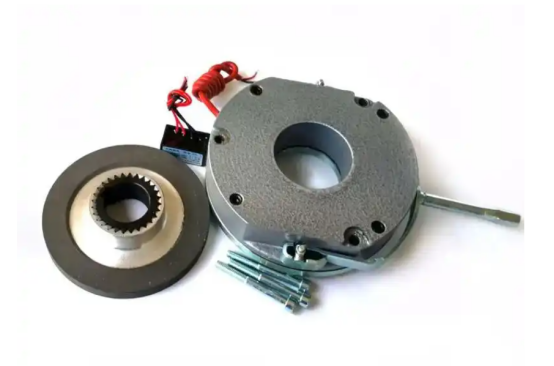
Crane Brake Inspection
Regular inspections are crucial for maintaining the safety and efficiency of crane brakes.
Overall Inspection
Inspect the entire brake system for smooth operation. Subsequently, check the contact condition of the brake electromagnet core. During the electromagnetic inspection, the flexibility of the magnet core can be tested by pressing it with a wrench. The brake arm should be rocked to observe any signs of wear, and it should be repaired or replaced regularly as it is a major wear part.
For long-stroke brakes, the stationary and dynamic iron cores can be inspected using the cement layer exclusion method (implemented at the bottom of the brake). Special cement can also be used to increase the firmness.
Brake Band Inspection
The brake band, serving as a transmission part and a critical wear surface in the braking system, necessitates periodic inspections. Check that brake band rivets are not protruding,as this causes critical destruction or excessive wear to the brakes and can lead to failure or bending of the components. This indicates that the wear state of brake bands needs attention and they ought to be proactively replaced.
Brake Wheel Inspection
As a critical component of the drive system, the brake wheel must be inspected regularly to ensure its integrity. Due to long-term contact with the brake band and the bearing of heavy loads, the brake wheel is prone to cracking. If cracks are found, the wheel must be replaced.
During inspection, pay particular attention to the taper hole and shaft areas to ensure their tightness. If looseness is detected, the components should be disassembled for inspection. After inspection, the brake wheel should be cleaned with kerosene to prevent accidents caused by oil or contaminants.
Additionally, a temperature sensor can be installed on the drive device to ensure that the operating temperature of the brake wheel remains below 200°C.
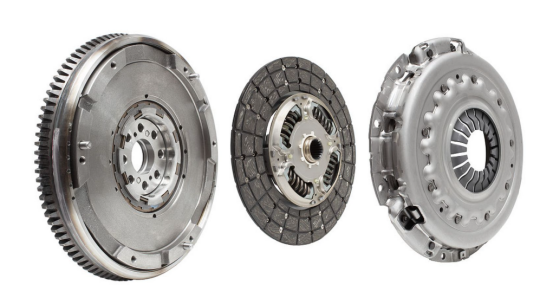
Crane Brake Troubleshooting
Due to the complex internal structure of brakes, failures can occur during prolonged use. It is necessary to troubleshoot these failures and adopt appropriate maintenance methods or replacements to ensure the performance of the crane in actual use.
Insufficient Braking Force
Inadequate braking force, an all too common problem during crane operations, can be caused by a number of things- almost always relates to problems concerning the brake wheel. The braking mechanisms loose springs, dirt, or inadequate lubrication may greatly impact the cranes overall function while also wearing down slowly on the brakes themselves. Due to importance of safety that revolves around the brake wheel, it becomes crucial for them to undergo thorough inspections.
Sudden Brake Failure
During the daily use of cranes, sudden brake failures can occur, which is very dangerous and can lead to high-altitude falls.
The main cause of brake failure is the brake band, usually due to brake pad detachment or spring failure. Although the probability of brake damage is relatively low, it can still occur.
When troubleshooting this type of problem, it is usually necessary to replace or repair damaged components, such as the brake band, and adjust the relevant parameters of the brake to ensure that the operating parameters meet the actual application standards, thereby improving production safety.
Excessive Brake Wheel Temperature
The operating temperature of a brake wheel should not exceed 200°C, but continuous friction caused by unreleaseable brakes due to overcentering or misalignment on the systems can heat the brake wheel up to above 300°C within five minutes. This excessive temperature results in smoking of the brake band.
To mitigate this problem, the gaps on both sides should be equalized and proper placement of the breaking torque surfaces achieved so that they are parallel when adjusted. Doing such will result in centered positioning of the band and thus better alignment between the band and wheel ensuring proper adjustment.
Inability to Open Brake Arm
During normal crane operation, the brake arm may fail to open when activated. The main causes of this problem include malfunctions of the various hinge points, circuit failures or breaks during operation, insufficient voltage, and burned coils or rectifier components.
A thorough inspection is required for these problems. During regular servicing of the brake caliper, care should be taken to ensure that all pivot points are adequately lubricated with light oils so as to minimize wear on the brake arm and stave off inoperable functionality.
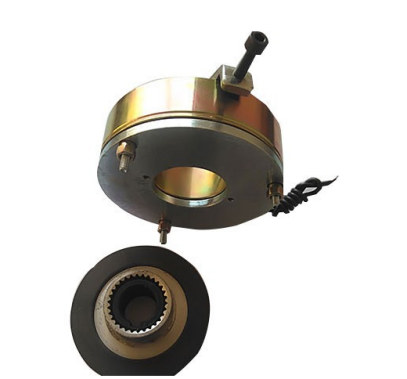
Selecting the Right Brake Coil for Crane
Appropriate choice, examination, and servicing of crane brakes is crucial for the safety and productivity of crane operations. Consideration of design principles, safety factors, and possible concerns enables proper maintenance and operation which increases uptime while minimizing accidents.
CPTC is a dedicated manufacturer in the domain of spare parts tower cranes as a professional providing detailed tower crane spare parts. If you have queries regarding selection of brakes for your cranes, do not hesitate to get in touch with us.
Related Products
High Quality Crane Operator Cabin for Tower Crane
High quality steel material for frame
The cab is…
Crane Cabin
Condition:100%new
Color:as your depend
Application:Tower Crane
Fishing Plate for Tower Crane Fixing Angle
All Kinds of Tower Crane Fixing Angle
Good stability
Lightweight