Tower cranes are indispensable in modern construction, playing a crucial role in lifting and transporting heavy materials. The efficient and reliable operation of these machines heavily relies on the integrity of their electrical systems.
This article will delve into the key components of tower crane electrical systems, outline essential maintenance practices, and explore common faults and their troubleshooting methods.
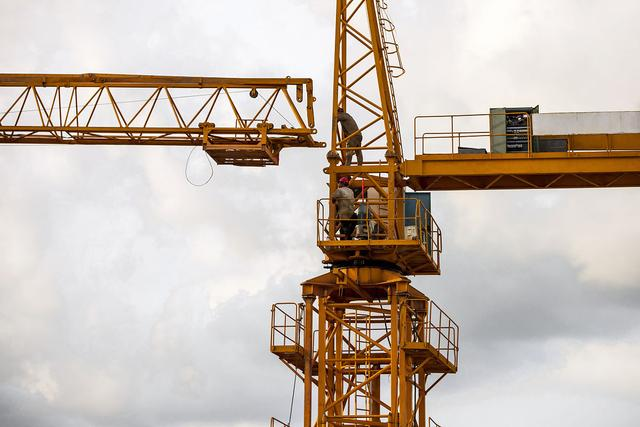
What are The Main Electrical Components of a Tower Crane?
The electrical system of a tower crane encompasses a wide range of components that work in conjunction to control various functions, including hoisting, slewing, luffing, and traveling. Some of the key electrical components include:
Motors:
Tower crane motors are the core components of a tower crane’s electrical system. They are primarily responsible for powering the crane’s various operations.
Tower crane motors can be primarily categorized into three types: hoisting motors, slewing motors, and luffing motors. Hoisting motors are responsible for raising and lowering the crane’s main boom, slewing motors control the rotation of the main boom, and luffing motors are used to adjust the length of the crane’s boom.
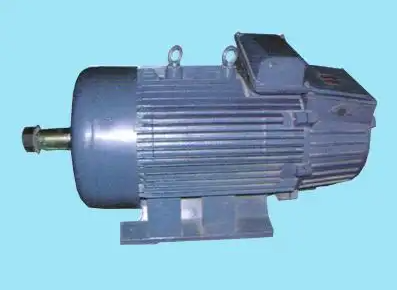
Controllers:
The tower crane controller is another core component of the tower crane’s electrical system, primarily responsible for regulating and controlling the tower crane’s motors.
Controllers are divided into primary and secondary controllers. The primary controller is responsible for controlling and regulating the entire tower crane, while the secondary controller controls the auxiliary parts of the tower crane, such as lights, alarms, and hydraulic valves.
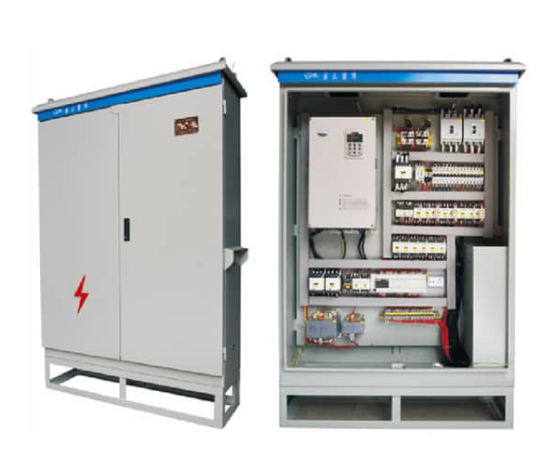
Sensors:
Tower cranes are equipped with various sensors, including load cells to measure the weight of the lifted load, wind speed sensors to monitor wind conditions and prevent operation in hazardous conditions, and position sensors to track the position of the jib and trolley.
Electrical Wires and Cables:
Electrical wires and cables are crucial components of a tower crane’s electrical system. They are responsible for transmitting electrical power and signals, ensuring the smooth operation of the crane.
Electrical wires and cables can be categorized into three types: power cables, control cables, and signal cables. Power cables primarily connect the tower crane’s electrical system to the power source. Control cables link the crane’s controller to the motors, while signal cables transmit data related to the crane’s operational status.
Maintenance and Inspection Points for Tower Crane Electrical Systems
During the daily operation of tower cranes, mechanical systems often exhibit excessive noise and overheating due to a lack of maintenance. Electrical system failures, on the other hand, are more difficult to observe directly and may not have obvious precursors.
Since most sudden breakdowns in tower cranes originate from electrical system issues, it is imperative to implement proactive maintenance and care for the electrical system to prevent electrical failures. Key maintenance and inspection points include:
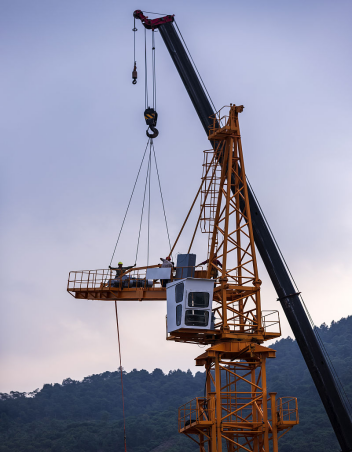
(1) Lightning Protection:
- Regularly inspect and maintain grounding systems.
- Ensure proper installation and functioning of lightning arresters.
- Conduct periodic earth resistance tests.
(2) Rainproofing:
- Regularly inspect and repair any damage to electrical enclosures and wiring due to rain or moisture.
- Ensure proper sealing of all electrical connections.
- Use weatherproof materials for all outdoor electrical components.
(3) Pollution Prevention:
- Keep the electrical equipment clean and free from dust, debris, and other contaminants.
- Regularly clean electrical enclosures and connectors.
- Use appropriate covers and enclosures to protect electrical components from environmental pollution.
(4) Regular Tightening:
- Regularly check and tighten all electrical connections, including terminal blocks and cable clamps.
- Prevent loose connections that can lead to arcing, overheating, and equipment failure.
Common Faults and Troubleshooting Methods for Tower Crane Electrical Systems
When an electrical fault occurs, the first step is to determine which part of the system is malfunctioning. Generally, a malfunction in one mechanism will not affect the operation of other mechanisms. If multiple mechanisms fail simultaneously, it can be inferred that there is a problem with the main power supply, PLC, or certain components on the control panel.
Electrical faults are often hidden, and troubleshooting can be approached using a backward reasoning method. Common faults and their troubleshooting methods are described below:
(1) Power supply tripping or sparking at the variable frequency drive main power terminal:
- Possible causes: Loose connections, short circuit, overload, faulty wiring, ground fault.
- Troubleshooting:
- Visually inspect for loose connections, damaged insulation, or signs of overheating.
- Check for short circuits using a multimeter.
- Verify that the load does not exceed the rated capacity of the VFD.
- Inspect and repair faulty wiring.
- Check the ground connection for proper continuity.
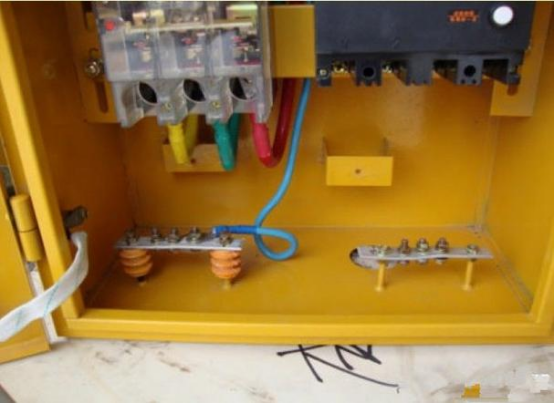
(2) No display after power supply:
- Possible causes: Power supply failure, control panel malfunction, communication issues, blown fuses.
- Troubleshooting:
- Check for power supply to the control panel.
- Inspect fuses and replace if blown.
- Check for any loose connections within the control panel.
- Verify communication between the control panel and other electrical components.
(3) No output after starting, motor does not start:
- Possible causes: Motor failure, faulty contactor, blown fuses, VFD malfunction, overload protection.
- Troubleshooting:
- Check for motor continuity and insulation resistance.
- Inspect and test the contactor for proper operation.
- Check and replace blown fuses.
- Check for any error codes or alarms on the VFD display.
- Verify that the load does not exceed the motor’s rated capacity.
(4) Variable frequency drive stops output:
- Possible causes: Overcurrent, overheating, voltage sag, communication errors, internal faults.
- Troubleshooting:
- Check for overcurrent conditions and address any overload issues.
- Check for proper cooling and ventilation of the VFD.
- Monitor the input and output voltage levels.
- Check for communication errors between the VFD and other control components.
- Refer to the tower crane manufacturer’s troubleshooting guide for specific error codes.
(5) No slewing action:
- Possible causes: Slewing motor failure, faulty slewing gear
- Troubleshooting: First, inspect the external connections to ensure they are correct. If the connections are fine, use a multimeter to measure the resistance of the resistor box and motor terminals to determine if there is a short circuit or ground fault.
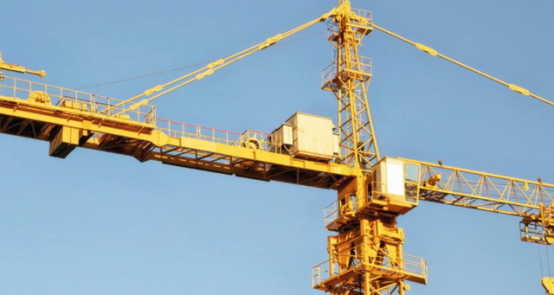
Safety First, Prevention is Key
Tower crane safety inspections are crucial for ensuring the smooth progress of construction projects and preventing accidents. Construction companies should strictly adhere to national regulations and standards to conduct regular and comprehensive safety inspections of tower cranes, ensuring their safe operation.
At the same time, it is essential to strengthen safety management on construction sites and enhance workers’ safety awareness to create a safe and stable construction environment.
Related Products
Tower Crane Trolley
Multiple functions
Intuitive operation
Tower Crane Trolley Mechanism
Hoisting Wire Rope for Tower Cranes
Wide variety of specifications
Casting Tower Crane Pulley
High strength;…
Crane Cabin
Condition:100%new
Color:as your depend
Application:Tower Crane