Wire ropes serve as indispensable tools in lifting and hauling equipment across a wide range of industries. Over time, these ropes undergo wear, corrosion, and other forms of degradation, necessitating a rigorous maintenance regimen that includes regular inspections and timely replacements to ensure optimal performance and safety.
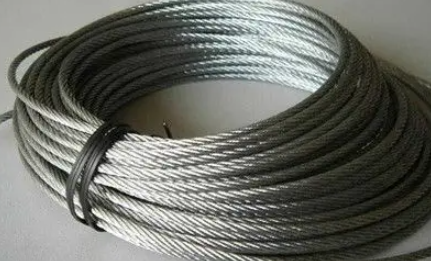
Factors Affecting the Replacement Cycle of a Wire Rope
The replacement cycle of a wire rope is not fixed but is influenced by a combination of factors. Firstly, the material of the wire rope itself plays a significant role. The type of steel used affects the rope’s lifespan. Load conditions, such as heavier loads or frequent shock loading, accelerate wear.
Secondly, the operating environment has a substantial impact. Wire ropes in frequent use wear out more quickly, necessitating more frequent replacements. Adverse conditions such as high temperatures, humidity, and corrosion accelerate wear and corrosion.
Finally, the quality of maintenance and lubrication directly affects the service life of a wire rope.
Wire Rope Factors
- Material and Structure: The type of steel, wire diameter, strand configuration, and lay significantly influence a wire rope’s strength, flexibility, and resistance to wear and corrosion. High-quality steel, proper stranding, and appropriate lay contribute to longer service life.
- Manufacturing Process: The manufacturing process, including wire drawing, stranding, and rope forming, impacts the rope’s quality and consistency. Precise manufacturing techniques and stringent quality control measures ensure a reliable product.

Operating Environment Factors
- Load Magnitude and Frequency: Heavy loads and frequent cycles accelerate wear and fatigue. Reducing the load or frequency of operation can extend the rope’s life.
- Temperature Extremes: Exposure to high or low temperatures can degrade the rope’s strength and flexibility. Maintaining optimal operating temperatures can mitigate this effect.
- Corrosive Environments: Exposure to corrosive substances like saltwater, acids, or alkalis accelerates corrosion. Implementing corrosion protection measures, such as coatings or regular cleaning, can mitigate this issue.
- Bending Stress: Frequent bending, especially over small sheaves or drums, induces fatigue. Using larger-diameter sheaves and minimizing bending radii can reduce stress and prolong the rope’s life.
Maintenance Factors
- Lubrication: Inadequate or improper lubrication increases friction and wear. Regular lubrication with a suitable lubricant can reduce friction and protect the rope from corrosion.
- Inspection Frequency: Regular inspections help identify and address wear, corrosion, and broken wires early on. A well-defined inspection schedule can prevent catastrophic failures.
- Operating Procedures: Adherence to proper operating procedures, such as avoiding shock loads and overloads, minimizes damage. Training operators on proper usage can significantly extend the rope’s life.
Equipment Factors
- Drum and Sheave Condition: The condition of drums and sheaves, including diameter, groove shape, and surface finish, affects wire rope life. Ensuring that drums and sheaves are properly maintained and free of damage can prevent premature rope wear.
- Guiding Devices: Proper alignment and maintenance of guiding devices prevent excessive wear and damage. Regular inspection and adjustment of guiding devices can help maintain optimal rope performance.
Other Factors
- Shock Loads: Sudden, high-impact loads can cause localized damage and fatigue. Avoiding shock loads, such as sudden starts and stops, can extend the rope’s life.
- Vibration: Continuous vibration can accelerate fatigue and wear. Reducing vibration sources or isolating the rope from vibration can mitigate this issue.
- Improper Installation: Incorrect installation can lead to stress concentrations and reduced service life. Proper installation, including tensioning and alignment, is crucial.
General Principles of Wire Rope Replacement
As a critical component of lifting equipment, wire ropes play a vital role in ensuring overall operational safety. Therefore, timely replacement of aged or damaged wire ropes is essential for safe production. Under normal operating conditions, the service life of a wire rope is typically one to three years. However, this is only a general guideline, and the actual replacement time should be determined based on specific circumstances. To ensure safety, it is recommended to inspect wire ropes regularly. Once severe wear, cracks, or deformation is detected, the wire rope should be replaced immediately.
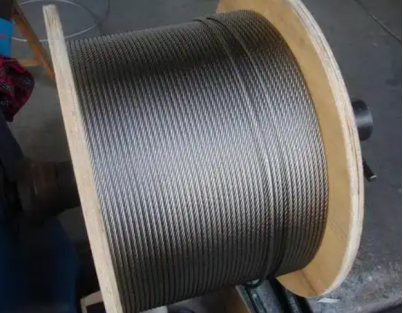
Regular Inspection
- Visual Inspection: Check for broken wires, wear, corrosion, and deformation.
- Dimensional Measurement: Measure the rope diameter to assess wear.
- Performance Testing: Conduct tensile and bending tests to evaluate strength and flexibility.
Criteria for Discarding
- Broken Wires: Replace if the number of broken wires exceeds the manufacturer’s or industry-standard limits.
- Wear: Replace if the rope diameter is significantly reduced or if there is severe localized wear.
- Corrosion: Replace if corrosion has compromised the rope’s strength or flexibility.
- Deformation: Replace if the rope is kinked, birdcaged, or otherwise deformed.
Replacement Timing
- Periodic Replacement: Replace at regular intervals based on usage, environment, and manufacturer’s recommendations.
- Failure Replacement: Replace immediately if the rope fails or is severely damaged.
- Inspection Replacement: Replace based on inspection findings, even if the rope has not reached its expected service life.
Replacement Precautions
- Select the Correct Rope: Choose a replacement rope with the same specifications as the original.
- Proper Installation: Install the rope correctly, avoiding twists and kinks.
- Lubrication: Lubricate the new rope to reduce friction and wear.
How to Extend the Service Life of a Wire Rope
To extend the service life of wire ropes, the following measures can be taken: carefully select the type and specification of the wire rope to ensure its load-bearing capacity matches the actual demand; strengthen maintenance and inspection, and replace severely worn wire ropes in a timely manner; improve the operating environment, and avoid exposing the wire rope to harsh conditions. The following are detailed maintenance regulations.
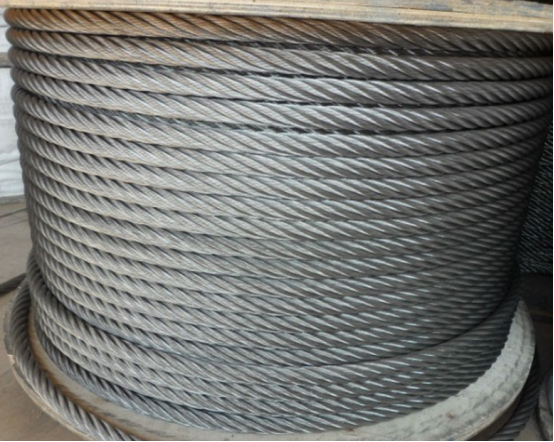
Selection and Installation
- Quality Assurance: Choose a wire rope from a reputable manufacturer that adheres to industry standards. Ensure the rope’s material, construction, and specifications are suitable for your specific application.
- Proper Fit and Installation: Select a rope with the correct diameter and construction to fit your equipment. During installation, avoid sharp bends, kinks, and excessive tension.
Regular Inspection and Maintenance
- Visual Inspection: Regularly inspect the rope for signs of wear, such as broken wires, corrosion, and excessive wear on the outer wires.
- Diameter Measurement: Periodically measure the rope’s diameter to assess wear.
- Lubrication: Apply a suitable lubricant to the rope at regular intervals to reduce friction and prevent corrosion. The type of lubricant should be selected based on the operating environment.
- Avoid Overloading: Never exceed the rope’s rated load capacity. Overloading can lead to premature failure.
- Minimize Shock Loads: Avoid sudden, high-impact loads, as they can damage the rope’s internal structure.
- Inspect for Corrosion: Regularly check the rope for signs of corrosion, especially in harsh environments.
- Store Properly: When not in use, store the rope in a dry, cool place, away from direct sunlight and moisture.
Operational Considerations
- Drum and Sheave Condition: Ensure that drums and sheaves are properly aligned and free of damage. Damaged drums and sheaves can accelerate rope wear.
- Avoid Sharp Bends: Minimize the number of sharp bends in the rope to reduce stress and fatigue.
- Proper Tensioning: Maintain proper tension in the rope to prevent slack and excessive stress.
- Environmental Factors: Minimize exposure to harsh environments, such as extreme temperatures, corrosive chemicals, and excessive moisture.
- Timely Replacement: Replace the rope when it reaches its service life or shows signs of significant wear or damage.
In conclusion, the replacement cycle of wire ropes is influenced by numerous factors and requires evaluation and decision-making based on specific conditions in actual use. Therefore, to ensure operational safety, users should regularly and comprehensively inspect wire ropes for damage and replace damaged ones promptly. When selecting new wire ropes, it is essential to ensure that they are made of the same material, have the same diameter, and are the same length as the original ropes. Additionally, a comprehensive risk assessment should be conducted before replacing wire ropes.
Related Products
Wire Rope
High Tensile Strength and Durability
Compliance with Safety…
Safety Rope
Lightweight and Portable
Durable and Long-lasting
Hoist Gearbox
Stable and reliable operation, secure
High flexibility, adjustable speed
Wide range…
Bronze & Brass Worm Wheel
Precise control for smooth operation
Simple…